TOOLING FABRICATION OVERVIEW
Tooling fabrication is the prime consideration in making good products. Consider this: If you design and build great tooling, you can make great products; however, poorly made tooling never produces a great product!
Source International is a leader in tooling fabrication, design, and engineering. We offer our customers better tooling designs with competitive pricing and always the highest quality, with long usable life. Our diverse knowledge and craftsmanship in tooling fabrication and in building all types of production molds, dies, and jigs, means we can offer the right tooling fabrication solutions. As your full-service provider of production molds, tooling and jigs, our expert project managers integrate product development and manufacturing to deliver custom OEM products ready for mass production. Our commitment is to always deliver quality, innovation, and reliability.
Tooling Fabrication and Mold Making
Tooling fabrication is a core competency at Source International. You see, we have no products of our own. All our production is custom produced to our specifications, and in most cases this requires custom-made molds, tooling, and production jigs to be developed. Our molds and tools are all precision made using the best materials and the latest technologies. We make molds for our own production, and we also make molds for export to others. Below are just a few of the types of tooling that we make:
- Injection Molds
- Casting & Forging Molds
- Compression Molds
- Extrusion Dies
- Stamping Tools
- Production Jigs
- EDM, Wire Cutting, CNC
- DME or Metric Standards
It all starts with the design of the tool. Our tooling fabrication engineers are committed to continuous improvement and use the latest CAD/CAM systems to meet the ever-changing needs of our customers. Our customers rely on us for advice in all phases of their tooling fabrication requirements, and we deliver!
The product part cost is highly influenced by the design of the mold, and our mold engineers provide the creative input necessary to make the best possible decisions, giving confidence, peace of mind, and reliability.
Over the years, Source International has earned the trust of the toughest, most demanding customers in the business—mold by mold. Our engineers understand the demands of today’s exacting tooling requirements.
ONCE THE TOOLS ARE COMPLETED, WE BEGIN MASS PRODUCTION AND OUR QUALITY ASSURANCE WORK
OUR WORLD CLASS TOOLING WORKSHOP
Whatever your tooling application requires, at Source International we do it all…and we do it better. We combine an experienced design and engineering team with highly advanced technology and best-in-class equipment. At every step, you can expect superb consultation, attention to detail and customized services that meet your needs. We produce quality results and keep you updated every step of the way.
Our attention to detail in tooling fabrication and our manufacturing experience and knowledge give you an edge to create precision components with component interchangeability to lower maintenance costs, increase mold life, and provide more consistent product quality.
Scroll through our photo gallery to see for yourself the quality of our tooling fabrication equipment and workmanship.
Injection Molds
Injection molding tooling is a lifeline for injection molding. The primary goal of custom tooling and fabrication is to develop a product with high manufacturability.
Plastic injection tooling can be used to determine the quality of the injection molding process and the resulting products, ranging from simple parts to complex applications.
Tooling fabrication utilizes metal molds or “tooling” to shape molten plastic resins. The tooling is typically made of aluminum, steel, or alloys and consists of two halves. Complex tooling can also include internal components with the following:
- Alignment Devices
- Bushings
- Ejectors
- Guides
- Lifters
- Pins
- Slides
The selected mold components and material must be compatible with the injection material to ensure dimensional tolerances are met and to promote product longevity.
Casting & Forging Molds
Tooling fabrication is vital to the various metal casting processes used to manufacture components for the most demanding industries, including petrochemical, defense, aerospace, and more.
Our tooling fabrication engineers employ the latest CAD/CAM systems to meet our customers’ specific needs, offering expert advice in all phases of the custom tooling and fabrication process. We use quality tooling to construct molds for metal casting. The molds we produce can be used once or for multiple mold technologies.
Product part costs are largely determined by the mold design. Our engineers can provide the necessary creative input to instill confidence and peace of mind in our customers. We make sure every metal casting is precise, efficient, and fail-proof, which is critical in corrosive or otherwise harsh environments.
Compression Molds
At Source International, we can manufacture single and multiple-cavity compression tools used to mold the following:
- Composites
- Substrates
- Thermoform
- Thermoset Sheet Stock
We offer deep expertise in the manufacture of complex, multi-side compression molds requiring precision tolerances. Our compression molds can pressure form substrate layers while edge trimming the finished piece in one run.
Compression molding uses a measured amount of preheated molding material (a charge) that gets compressed using two heated molds to achieve the desired form. The multi-step process involves:
While similar to injection molding, compression molding uses molds that get closed around the charge instead of being injected into a closed mold cavity. Compression molding is an ideal solution for creating simple designs and large basic shapes that cannot be easily created using extrusion techniques.
Extrusion Dies
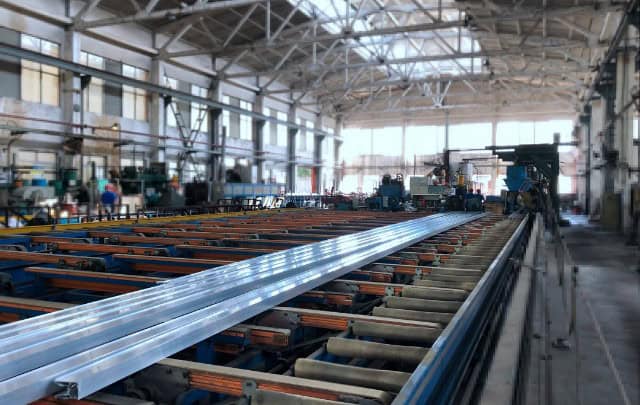
The lead time and initial costs of extrusion tooling are usually considerably lower than the tooling costs associated with alternative technologies such as:
- Die Casting
- Impact Extrusion
- Pultrusion
- Stamping
- Steel Roll Forming
- Vinyl Extrusion
A typical extrusion operation utilizes a die and die assembly held together by a tool carrier. The die is usually an H13 steel disk with an opening that resembles the desired cross-section of the final extruded product.
A combination of hollow, semi-hollow, or solid shapes can be incorporated into a single die. All types are easy to manufacture, cost-effective, and suited for CNC machining.
Metal Stamping Tools
Short-run metal stamping requires minimal upfront tooling expenses and is ideal for small projects and prototypes. The smaller run size and custom-forming operations can result in a higher per-piece charge. However, the absence of tooling costs makes short runs more cost-efficient, especially for projects requiring a quick turnaround.
Metal stamping converts flat metal sheets into a desired shape utilizing a complex manufacturing process. This process can include metal forming techniques such as:
Bending
Blanking
Piercing
Punching
Once the process has been confirmed, you can enjoy a cost-effective solution that offers high quality, durability, and fast turnaround times.
Production Jigs
While tooling, jigs, and fixtures can serve different purposes in the manufacturing process, they share common functions and characteristics. Distinguishing these tools is crucial for optimizing production processes and reducing costs while maintaining quality.
A production jig is used to secure and guide a workpiece throughout the manufacturing process. This tool is commonly used in grinding, cutting, and drilling operations to ensure the workpiece remains stable, which is crucial for producing precise, accurate results. Jigs can be complex or simple, depending on the demands of the manufacturing process.
EDM / Wire Cutting / CNC
Wire EDM tooling is a unique processing technology commonly used in industrial production. Unlike traditional methods that require mechanical energy for cutting, this non-contact subtractive technology uses heat generated by the discharge of electrical sparks to cut and remove material.
EDM wire cutting is not limited to a certain material. Since no significant mechanical or physical forces are used during cutting, this technology can be used to create complex shapes and designs with any conductive material.
Many parts manufacturers across various industries use this method, especially with CNC machinery, to produce parts considered unsuitable for conventional machining processes.
The following industries utilize wire EDM machines for processes ranging from prototyping to complete production runs:
- Aerospace
- Automotive
- Medical
DME or Metric Standards

DME molds are the standard in the U.S. DME molds may include throat teeth, threaded teeth, and nipples, whereas British teeth are PT. Compared to DME’s 55-degree tooth shape, the NPT form has a tooth shape of 60 degrees.
The DME standard has a broad range of products, including but not limited to:
- Hot Runner System Injection Molding Series
- Intelligent Temperature Controller
- Mold Temperature Control System
Contact Source International For Your Tooling Fabrication Needs
Source International offers custom tooling fabrication services for a wide range of industries and applications. Our experienced engineering and design teams utilize cutting-edge technology and best-in-class equipment to provide quality services that can meet the specific demands of your next project.
Contact us to learn more about our tooling expertise or with questions about our tooling fabrication capabilities.